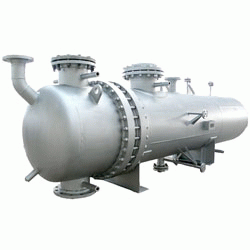
shell and tube heat exchanger. It is the most common type of heat exchanger
in all Industries. Mostly used in higher-pressure and Higher Temperature
applications.
This types of Heat
exchangers are having two divisions one is shell and other is Tubes. Here One
fluid runs through the tubes, and another fluid flows over the tubes (through
the shell) to transfer heat between the two fluids. For this purpose
seamless/ERW or Rolled pipes are used for shell. And Seamless tubes are used
for Tubes.
Our Shell and Tube Heat
Exchangers Design Process Contains Two Parts - Thermal and Mechanical Design
Part A - Thermal
Design
·
1. Consideration of Process Fluids in both Shell and Tube Side,
·
2. Selection Of Required Temperature Specifications,
·
3. Limiting the Shell and Tube side Pressure Drop,
·
4. Setting Shell and Tube Side Velocity Limits,
·
5. Finding Heat Transfer Area Including Fouling Factor.
·
Part B- Mechanical Design
·
1. Selection of TEMA Layout – Based on Thermal Design
·
2. Selection of Tube Parameters – Size, Thickness, Layout, Pitch,
material
·
3. Limiting the Upper and Lower Design on Tube Length
·
4. Selection of Shell side Parameters – Material Baffle Cut,
Baffle Spacing, and Clearances
·
5. Thermal conductivity of tube material.
·
6. Setting upper and Lower Design Limits on Shell Diameter, Baffle
Cut, Baffle Spacing.
Shell and tube heat exchanger is One type of Closed Circuit cooling Equipment.
For further detail please contact:
For CBRO
INCORPORATION
Mobile no. : 09930531628 / 09173809999
Email: cbro_sales@hotmail.com